INSPECTION
CAPABILITIES
INSPECTION
NDT – EDDY CURRENT & ULTRASONIC TESTING
NDT inspection processes are an important part of Bar Processing Corporations capabilities in the industry, and for the past 30 years we have provided unsurpassed inspection services. Product inspection capabilities utilizing ultrasonic, eddy current, encircling coil, demagnetization, and grade verification technologies are used to assure both surface and internal quality requirements.
Eddy Current Rotary Probe
A Non Destructive Testing (NDT) technique commonly used for inspecting the surface of steel bar products. This method leverages the principles of electromagnetism to detect surface defects (typically seams), measure material properties, and ensure product quality without causing any damage. Testing is preformed to customer specified criteria on length and depth down to 0.005” max.
Ultrasonic
Non Destructive Testing (NDT) is a widely used technique for evaluating the internal and/or surface integrity of steel bar products. Ultrasonic testing utilizes high frequency sound waves to detect internal flaws, measure thickness, and assess material properties to customer specifications in a non destructive manner, meaning it does not alter or damage the material being tested.
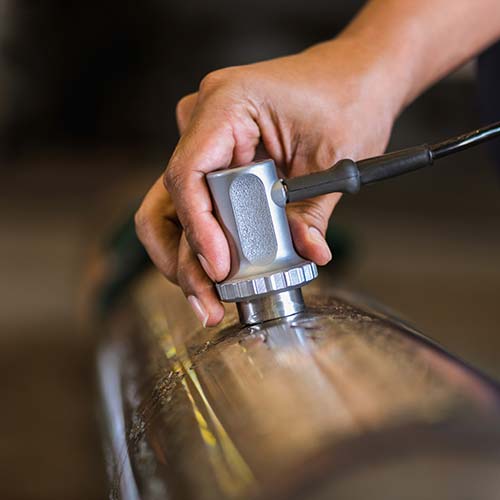
Grade Verification or Spectro Testing
A type of non destructive testing (NDT) that evaluates the chemical composition of steel bar products. This process helps to ensure that the material meets the specified standards and the correct grade of steel is being used for the intended application and prevent mixes.
Bar Processing Corporation, under the direction of its Level III Manager of NDT, has the ability to:
1. Design specific inspection criteria utilizing specialized equipment.
2. Develop testing and inspection procedures to customer specific requirements.
Bar Processing Corporation NDT inspectors are trained and certified to Level I & Level II in accordance to SNT-TC-1A, 1992 edition.
BPC also provides numerous additional quality assurance functions:
- Product Straightness
- Dimensional Control
- Surface Roughness
- Optical Comparison
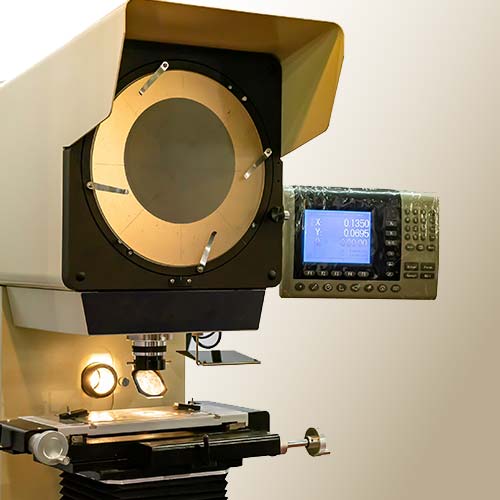
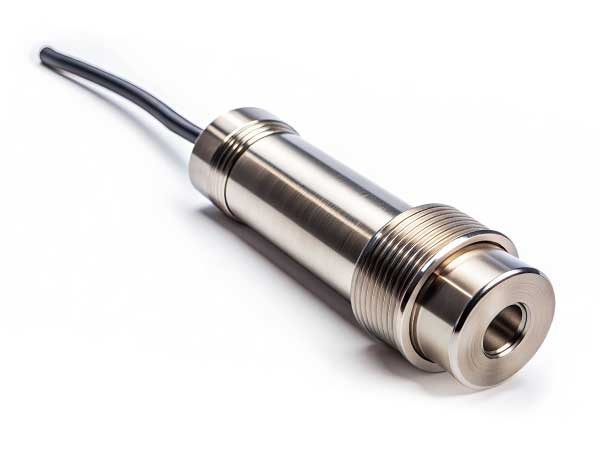
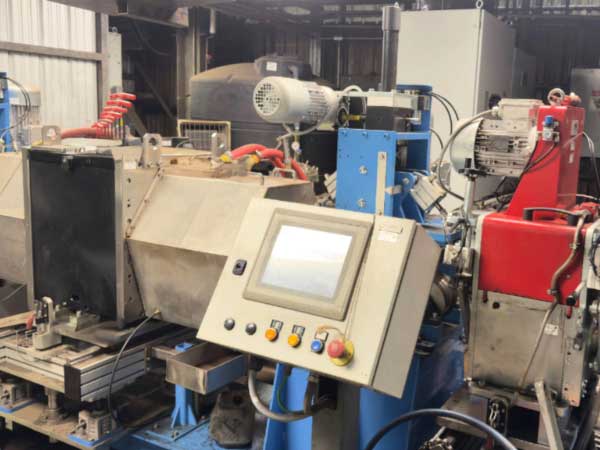
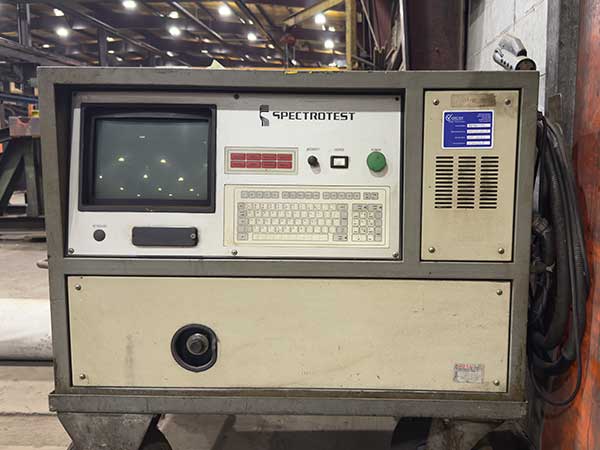
Process | Warren, Michigan | Monroe, Michigan | Newton Falls, Ohio | Wickliffe, Ohio | Chicago Hts., Illinois |
---|---|---|---|---|---|
EDDY CURRENT INSPECTION | |||||
MIN/MAX DIAMETER | 0.700″ – 4.000″ | 0.781″ – 3.125″ | 0.500″ – 5.125″ | 0.700″ – 5.250″ | 0.750″ – 3.437″ |
MIN/MAX LENGTH | 8′- 40′ | 10′- 38′ | 10′- 35′ | 12′- 50′ | 10′- 30′ |
ULTRASONIC INSPECTION | |||||
MIN/MAX DIAMETER | 0.718″ – 4.000″ | 0.781″ – 3.125″ | 0.500″ – 5.125″ | 1.000″ – 5.125″ | 0.718″ – 2.9375″ |
MIN/MAX LENGTH | 8′- 40′ | 10′- 38′ | 10′- 40′ | 12′- 50′ | 10′- 32′ |
HAND HELD UT >4.000″ | HAND HELD UT >3.125″ | HAND HELD UT >5.125″ | HAND HELD UT >3.125″ | HAND HELD UT >2.9375″ | |
GRADE VERIFICATION (SPECTROMETER) | |||||
✔ | ✔ | ✔ | ✔ | ✔ | |
Click Here to DOWNLOAD a Full Capability Summary by Location |